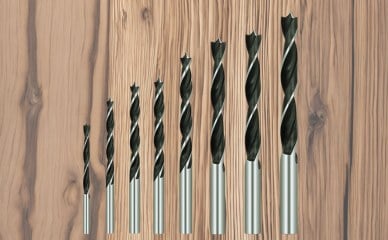
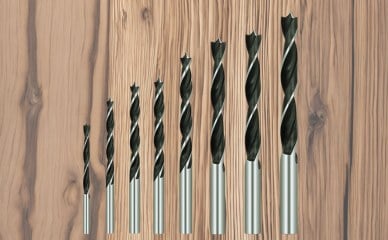
Ever watched your CNC router massacre a beautiful piece of walnut because of a poorly planned toolpath? It’s like witnessing a slow-motion train wreck—painful and expensive. We’ve all been there: hours spent designing, setting up, and then… disaster. The culprit? Inefficient toolpaths that waste time, break bits, and produce subpar results.
But fear not. This post is your roadmap to mastering CNC router toolpaths, ensuring your projects are efficient, precise, and, most importantly, successful.
Poorly optimized toolpaths often result in unnecessary movements—think of your router taking the scenic route when a direct path would suffice. This not only increases machining time but also accelerates tool wear.
Random or erratic toolpaths can lead to inconsistent surface finishes. Instead of a smooth, professional look, you get a patchwork of textures that scream amateur hour.
Inefficient toolpaths can cause your router to engage material at suboptimal angles or depths, leading to increased stress on the tool and premature wear or breakage.
Complex or convoluted toolpaths increase the likelihood of errors—missed steps, incorrect depths, or even collisions. Each mistake is a potential project killer.
Start with the end in mind. Determine the most efficient sequence of operations to minimize tool changes and repositioning. Group similar operations together and plan your cuts to reduce unnecessary movements.
Leverage CAM software that offers advanced toolpath optimization features. Programs like Fusion 360 or VCarve Pro allow you to simulate toolpaths, identify inefficiencies, and make adjustments before cutting.
Adjust your feed rates and spindle speeds to match the material and tool you’re using. Proper settings reduce tool wear and improve surface finish. Refer to manufacturer recommendations and conduct test cuts when necessary.
Instead of plunging straight into the material, use ramp or helical entry moves. These approaches reduce stress on the tool and material, leading to cleaner cuts and longer tool life.
Ensure your toolpaths are designed to minimize retracts and non-cutting movements. Every moment the tool isn’t cutting is wasted time. Efficient paths keep the tool engaged as much as possible.
Consider a maker attempting to produce intricate wooden inlays. Initially, their toolpaths were inefficient, leading to tear-outs and inconsistent fits. By re-evaluating their approach:
The result? Cleaner cuts, reduced production time, and a product that met quality expectations.
Optimizing your CNC router toolpaths isn’t just about efficiency—it’s about elevating the quality of your work, extending the life of your tools, and ensuring every project meets your standards. By implementing strategic planning, leveraging the right software, and fine-tuning your approach, you can transform your CNC projects from frustrating to flawless.
Ready to take your CNC projects to the next level?
Stay tuned for the next post in our series, where we’ll delve into common CNC machining errors and how to avoid them.